- Introduction
- 1. Plan and Budget Wisely
- 2. Choose Cost-Effective Materials
- 3. Leverage Skilled Labor for Efficiency
- 4. Optimize Project Management
- 5. Implement Energy-Efficient Designs
- 6. Utilize Prefabricated Components
- 7. Negotiate with Suppliers
- 8. Adopt Lean Construction Practices
- 9. Engage in Value Engineering
- 10. Regularly Review and Adjust Plans
- Conclusion
- Detailed Project Planning: Outline each project phase with your construction team. This prevents unexpected expenses and keeps everyone aligned.
- Budget Allocation: Prioritize essential elements that cannot be compromised, such as the foundation and structural integrity, while considering alternative solutions for non-essential items.
- Contingency Fund: Always allocate 10-15% of your budget as a buffer for unforeseen costs.
For more on effective budget planning, visit our construction management tips.
Selecting appropriate materials significantly impacts your budget. Strategies include:
- Sustainable Materials: Opt for recycled or eco-friendly materials that are affordable and durable.
- Local Sourcing: Purchasing materials from local suppliers reduces transportation costs and supports the community.
- Comparative Shopping: Compare prices from different suppliers and negotiate for bulk purchase discounts.
Explore cost-effective building material recommendations for more information.
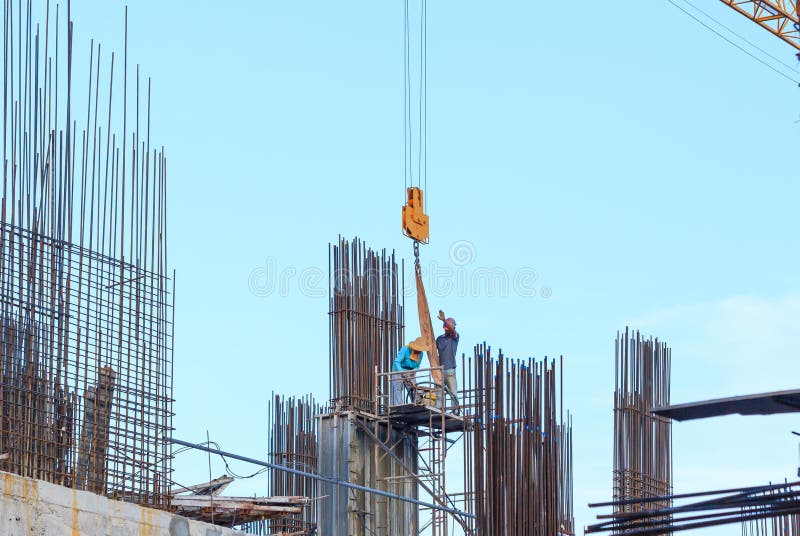
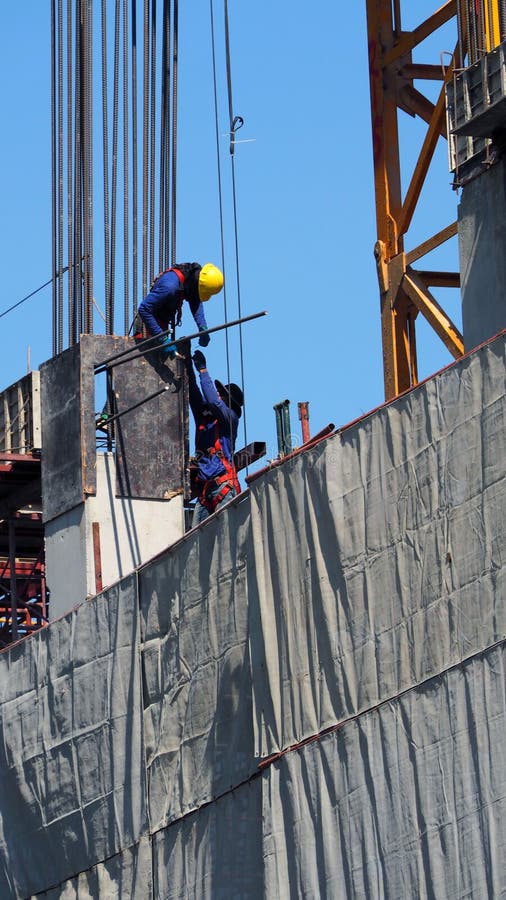

- Hire Experienced Professionals: Skilled workers may have higher hourly rates, but their efficiency and quality often lead to long-term savings.
- Cross-Training: Encourage workers to develop multiple skills, reducing the need for additional labor.
- Schedule Management: Handling shifts and working hours can avoid unnecessary overtime costs.
Learn how JMG Construction can support your projects with a skilled team in our services section.
- Bulk Purchasing: Buying in bulk often comes with discounts.
- Loyalty Programs: Long-term partnerships may result in better pricing.
- Competitive Bidding: Soliciting multiple quotes ensures competitive pricing.
- Efficient Resource Use: Only order materials as needed to reduce excess.
- Streamlined Processes: Eliminate unnecessary steps to improve efficiency.
- Continuous Improvement: Regularly assess and refine construction processes.
- Function Analysis: Determine the essential functions of a project to identify cost-effective alternatives without compromising performance.
- Material Substitution: Evaluate if more affordable materials can be used while maintaining durability and aesthetics.
- Design Adjustments: Collaborate with architects and engineers to modify designs cost-efficiently, such as simplifying structural layouts or reducing the number of unique components.
- Frequent Progress Checks: Conduct regular project reviews to compare current expenditures with the budget. Address any discrepancies promptly.
- Adapt to Changes: Be prepared to revise plans based on unexpected challenges or opportunities for savings. This proactive approach can help avoid costly overruns.
- Feedback Loop: Gather input from the construction team and stakeholders to identify areas for improvement throughout the project lifecycle.
